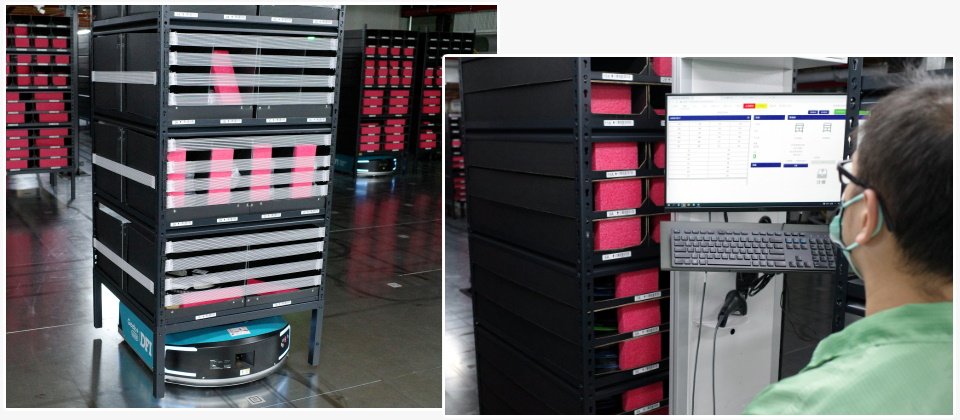
流程1 多工單合併接單,支援多種備料模式
單日30筆工單備料件數,每筆工單使用電子材料種類就有230種。當遇到有多筆PCB料號相同的工單,AS/RS自動化倉儲系統就會啟動多工單合併接單程序,讓具有相同料號的該批工單材料能一次集結,在分發到各自工單中,不用按一筆筆工單來揀。因為可使用系統接單,比起傳統人工備料,可以支援多種備料模式,提升工單備料效率。
流程2 靠AGV無人搬運車加快出料速度
AS/RS系統匯整所有工單後,就會按出單需求定位材料儲存位置以及規畫搬運順序,然後指派AGV無人搬運車執行揀料任務。AGV車接到指令後,就會靠倉儲地面的QR碼定位,駛至要搬運貨架下方,將其抬起,搬運至揀料工作站。貨架底部也有QR碼,AGV車移出貨架前會先確認貨架資訊正確後,再將其搬出。這座倉儲中最多一次能同時28臺AGV執行揀料任務。每趟搬運任務都能在2~5分鐘內完成。
流程3 專用AGV升降梯供垂直上下樓搬貨
倉儲內共有773座貨架,常用的電子材料會放在距離揀料站最近的貨架上,方便AGV車來搬運;至於使用頻率較少的材料或較大零件,則會放置於2樓夾層的貨架中。AGV要上樓前必須搭乘專用升降貨梯,才能上到2樓夾層將貨架搬出。AGV車來到升降梯前,門就會自動感應打開,進了電梯,等待AGV停到指定位置,電梯才關門上樓,全程都是自動化完成,不需要人為介入,下樓也是走同樣流程,再搬運至揀料站,排隊等待人員揀料。
流程4 揀料流程結合虛擬分揀播種牆
貨架送達揀貨站後,AGV車會自動發送通知給WMS系統,揀料員只要從觸控螢幕上按下確認,螢幕畫面裡播種牆的格子欄位,就會更新成現在貨架資訊,包括儲位格數和儲位編號,都與揀料員眼前的實體貨架格局一致,方便人員根據系統提示依序揀取。倉儲裡有三種類型的貨架,用於儲存各種尺寸的材料零件,每個貨架格局皆不同,對應到虛擬播種牆的格數也有所不同。
流程5 系統引導加快人工揀料速度
確認貨架類型後,揀料員會依據WMS系統的引導,從螢幕裡被標記為綠色的播種牆儲格,依序將工單所需的材料自貨架中取出。裝有材料的卷盤被取出後,人員會掃描料盤上的條碼,來確認螢幕上的材料資訊,並更新到系統資料庫記錄的該筆工單處理進度。一座貨架揀完後,AGV車會自動送貨架回倉儲原來位置,下一臺AGV就會移動到原本停放這臺AGV的位置,讓揀料員接續揀料。揀出來的料,會放置於備料架上等待做工單集結,再交由分料員進行剪料、分料動作。
流程6 依工單完成分料送到產線
這批工單備料材料集結後,會再由分料員依據生產工單清算材料盤數量,並依每張工單所需要的材料零件顆數,從每個料盤中進行剪料的動作。由於一個7寸材料盤約有3,000~10,000顆零件不等,因此目前這個作業環節,還是人工作業。如果是屬於高單價的材料零件,分料後多餘的料件就會再透過AGV車進行返倉動作。分料員分完所有材料後,會將這批料連同工單放置於備料臺車上,接著透過貨梯送上三樓,提供給SMT產線做生產使用。
熱門新聞
2023-12-03
2024-04-24
2024-04-25
2024-04-26
2024-04-22
2024-04-22
2024-04-22